l otro lado de la ciudad relojera de Le Locle, justo al lado de los molinos subterráneos de Col-des-Roches, se encuentra un edificio donde se producen materiales excepcionales. Comadur (contracción del francés “Composants en matériaux durs”) se especializa en producir componentes de dureza comprobada, que requieren tratamientos particularmente exigentes: cristales sintéticos (zafiro, rubíes), cerámica y microcomponentes. Esta entidad del Grupo Swatch es uno de los secretos bien guardados que permiten a la industria relojera Suiza seguir innovando en la investigación de materiales.
Uno de sus principales clientes dentro del grupo es Rado, cuyo lema es “Master of Materials”. Este campeón de la cerámica high-tech, que se presentó ya en 1986 en su modelo Integral (gracias a una colaboración con Comadur), produce relojes cuya textura recuerda a una segunda piel: sedosa, ultraligera y resistente a los arañazos, se adapta a temperatura corporal.
-
- La cerámica ha sido el centro de atención de Rado durante muchas décadas, como muestran nuestros propios archivos (un documento de 1991).
- ©Europa Star Archives
Pero la fabricación de cerámica de alta tecnología está lejos de ser fácil, ya que implica un procesamiento meticuloso de los polvos básicos y un dominio absoluto de las temperaturas de calentamiento de lo que es un material muy complicado de trabajar. Las raíces de Comadur, que emplea a más de mil personas en siete centros de producción en Suiza, se remontan a la consolidación de la industria relojera tras la crisis del cuarzo: la empresa fue creada en 1984 por la fusión de Seitz & Co, Méroz Pierres SA , Sadem SA y Watch Stones & Co SA, que a su vez fueron el resultado de varias fusiones sucesivas. La más antigua de ellas, Méroz Pierres SA, comenzó a fabricar joyas relojeras en 1880.
Esta entidad del Grupo Swatch es uno de los secretos bien guardados que permiten a la industria relojera suiza seguir innovando en la investigación de materiales.
Un tipo inusual de cerámica.
Para los varios millones de piezas de cerámica (principalmente cajas, esferas, biseles y brazaletes) que fabrica Comadur cada año, todo comienza con un proceso químico. La empresa calibra sus propias materias primas, en este caso, óxido de circonio (ZrO2), en forma de polvo. “La definición más amplia y básica de cerámica es un compuesto químico no metálico y no orgánico que se endurece al cocerse”, dice Oian Nicolas, CEO de Comadur. “Es una parte muy importante de la vida cotidiana, desde los azulejos hasta la cerámica. Sin embargo, nuestro enfoque de este proceso es de alta tecnología: utilizamos polvo de zirconio sintético extremadamente puro y fino para diseñar un material muy denso y no poroso, a diferencia de su cerámica, que no es 100 % impermeable”.
Se utilizan dos procesos de fabricación principales: prensado, donde se comprime el polvo; y el moldeo por inyección, el método más común utilizado en la producción de cerámica Rado. Esta técnica permite crear formas más complejas. El óxido de circonio se complementa con pigmentos resistentes a muy altas temperaturas, para dar color a la cerámica, así como polímeros (patentados por Comadur) para ayudar en el proceso de moldeo por inyección. “El proceso de fabricación de nuestra cerámica es muy delicado porque no se tolera ninguna contaminación, por pequeña que sea”, explica Oian Nicolas. “Por ejemplo, un rastro de hierro hará que el material salga amarillento”.
-
- Moldeo por inyección
El primer paso del proceso es definir cómo se puede fabricar la pieza para cumplir con el brief de diseño elaborado por la marca. Existe una gran limitación: durante el proceso de cocción, la pieza se encoge aproximadamente un 25% por efecto de la temperatura, algo que debe tenerse en cuenta a la hora de diseñar los moldes de inyección. El software de simulación se utiliza para probar cómo reaccionarán los materiales, a fin de crear el molde más preciso posible.
-
- Grabado láser
Una vez moldeadas, las piezas se colocan dentro de un horno y se exponen a una temperatura extremadamente alta (1.450°C) durante varias horas. Este proceso de sinterización endurece la cerámica y la transforma en su color final, al mismo tiempo que se evapora el polímero. Luego, el componente se mecaniza a sus dimensiones exactas, utilizando herramientas de diamante. A esto le sigue el pulido, sumergiéndolo en un baño que contiene fragmentos cerámicos que vibran a alta frecuencia; arenado, que crea un acabado mate; grabado láser de cualquier inscripción (como los números en el bisel), que luego se laquean; y finalmente, el control de calidad.
Existe una gran limitación: durante el proceso de cocción, la pieza se encoge aproximadamente un 25% por efecto de la temperatura, algo que debe tenerse en cuenta a la hora de diseñar los moldes de inyección.
Alquimistas contemporáneos
Gracias al trabajo de Comadur, Rado también pudo introducir nuevas cerámicas de colores en 2019, en los modelos True Thinline Les CouleursTM Le Corbusier, que van desde un intenso naranja brillante a un delicado siena pálido. Varios óxidos se mezclan con el polvo base para obtener los colores deseados, un sutil trabajo de alquimia contemporánea. “En cerámica, el negro es el color más sencillo de producir, paradójicamente mucho más que el blanco, aunque los compuestos químicos aparecen blancos al principio del proceso”, dice Oian Nicolas.
-
- Rado Captain Cook Chronograph
Rado también introdujo un nuevo acabado extraordinario, gracias a un efecto descubierto accidentalmente hace más de dos décadas: el plasma, que le da a la cerámica un aspecto metálico. Este efecto es particularmente apreciado en un momento en que la industria relojera está dominada por modelos sport-chic en acero. Comadur es una de las pocas entidades en el mundo que domina esta tecnología, que ve pasar el óxido de circonio bajo una antorcha de plasma que puede alcanzar los 20.000 °C (¡proteja sus ojos cuando los visite!), eliminando los átomos de oxígeno. La adición de carbono da como resultado la formación de carburo de circonio, otra cerámica, que tiene una apariencia similar a la del acero, pero conserva las ventajas de la cerámica: resistente a los arañazos, ligera, sedosa, hipoalergénica, duradera (a diferencia de un revestimiento de PVD , por ejemplo). Y sin nada de metal.
-
- Comadur es una de las pocas entidades en el mundo que domina la tecnología de plasma, en la que el óxido de zirconio pasa bajo una antorcha de plasma que puede alcanzar los 20 000 °C (¡proteja sus ojos cuando los visite!), eliminando los átomos de oxígeno.
Bajo el impulso de Rado, Comadur también ha desarrollado otras cerámicas como CeramosTM, un material compuesto por un 90% de cerámica de alta tecnología y un 10% de aleación metálica. Además, ha desarrollado cerámicas ultraligeras de alta tecnología utilizando nitruro de silicio. A lo largo del tiempo, la firma también ha experimentado con diferentes técnicas de decoración en sus cerámicas, que se pueden encontrar en las distintas marcas del Grupo Swatch: oro, barniz, Liquidmetal, Super-LumiNova®, incrustaciones de piedras preciosas, etc.
Rado también introdujo un nuevo acabado extraordinario, gracias a un efecto descubierto accidentalmente hace más de dos décadas: el plasma, que le da a la cerámica un aspecto metálico.
Varios millones de componentes de zafiro
La otra gran especialidad de Comadur es el zafiro sintético. Varios millones de piezas salen de sus diversos sitios cada año: la mayoría son cristales de reloj, pero la compañía también fabrica esferas y biseles. Aquí, el ingrediente básico es el óxido de aluminio. Una llama calentada a 2050°C funde el polvo de alúmina y, a medida que las gotas fundidas se solidifican, se forma un solo cristal cilíndrico, como una estalagmita. El resultado de esta operación, conocida como “método Verneuil”, es un monocristal de zafiro sintético, que luego se estabiliza antes de ser cortado con hilo de diamante para obtener los cristales de zafiro que se utilizan para proteger las esferas de los relojes. ¡En su sitio de Bad Zurzach, Comadur tiene no menos de 550 antorchas dedicadas a esta operación industrial!
Otro método para producir zafiro sintético, que tiene la ventaja de evitar cualquier pérdida de material durante la fabricación, se conoce como “EFG” (crecimiento alimentado por película definido por el borde). Se utiliza en particular para cristales que requieren geometrías, dimensiones y espesores específicos. Un crisol de metal, generalmente hecho de tungsteno o molibdeno, contiene un baño de alúmina fundida a partir del cual se genera el cristal de zafiro. Se sumerge una semilla en la superficie del baño, lo que provoca una solidificación local debido a la diferencia de temperatura entre la semilla y el baño. Luego, el cristal se forma por la acción de un movimiento ascendente, lo que permite que el material se solidifique a medida que sube.
-
- Rado Captain Cook High-Tech Ceramic
Comadur produce cristales de zafiro individuales en forma de placas de hasta 1,5 metros de largo, 15 cm de ancho y varios milímetros de espesor. Implementado en 2017, este método ha hecho posible reciclar varios años de material de zafiro no utilizado. Así, los residuos de un proceso se convierten en materia prima de otro. Este reciclaje de materia prima está en línea con el enfoque de sostenibilidad adoptado por Comadur y el Grupo Swatch.
Se producen muy pocos zafiros de colores, con la notable excepción de los rubíes, que pertenecen a la misma familia. maquinas CNC y se han desarrollado herramientas específicas con proveedores externos para manejar este complejo proceso. Se requieren entre 40 y 70 operaciones separadas para producir el cristal que protege la esfera del reloj. Hay disponibles varios acabados diferentes: antirreflejos, efecto fantasma, sensible al tacto (para el T-Touch), etc. Comadur produce más de 100 toneladas de zafiro al año mediante el proceso Verneuil y 25 toneladas mediante el proceso EFG.
Implementado en 2017, el método EFG ha hecho posible reciclar varios años de material de zafiro no utilizado. Así, los residuos de un proceso se convierten en materia prima de otro.
Donde la energía se encuentra con la materia
Desde Le Locle recorremos los 60 kilómetros que separan Comadur de la sede de Rado, en las afueras de Biel. Allí nos encontramos con Adrian Bosshard, un ex campeón de motociclismo suizo y una presencia de larga data en el Grupo Swatch. Después de 17 años al frente de Certina, asumió la dirección de Rado en 2020. Después de observar la producción de la cerámica que equipa la mayoría de los relojes de la marca, es fácil entender por qué Rado ha creado “una comunidad de clientes muy fiel ”, como apunta Adrian Bosshard. La sensación en la muñeca es tan única que no dejará indiferente a nadie: puede que algunos no quieran llevar otra cosa...
Para el hombre a cargo, el Capitán Cook High-Tech Ceramic lanzado el año pasado quizás represente mejor el éxito de Rado, en una era fascinada por los modelos históricos. Es una combinación de un diseño que data de hace exactamente sesenta años, que toma los códigos de moda del reloj de buceo, y un material que es el resultado de la tecnología de punta dominada por los ingenieros de Le Locle, produciendo una sensación refinada y muy contemporánea. . La ventaja de la cerámica es que no envejece, incluso si el diseño que encarna es en sí mismo vintage. También es un material tan único que realmente no se puede poner en ninguna categoría, lo cual es una buena noticia en una era que le ha dado la espalda a la clasificación.
-
- Presentado este año, el Captain Cook High-Tech Ceramic Diver es el resultado de las últimas técnicas de producción de cerámica de alta tecnología de Rado. Está disponible en seis variaciones diferentes (incluidas dos versiones de plasma).
Esta primavera, Rado lanzó un nuevo Capitán Cook Diver con certificación ISO y equipó su reloj insignia de 1962 con un cronógrafo. En este año de aniversario de la colección, la marca también presentó una edición limitada, el Captain Cook Over-Pole, un reloj de 37 mm con distintivos códigos vintage. Un lanzamiento estratégico en la segunda mitad del año fue el relanzamiento del Diastar Original, el reloj pionero resistente a los arañazos, particularmente reconocible gracias a su caja con forma. Nacido el mismo año que el Capitán Cook y un modelo clave de Rado, la marca ha producido y vendido continuamente el Diastar Original durante los últimos 60 años, lo que representa un total de más de cinco millones de piezas a lo largo de las décadas.
-
- En 1962, Rado presentó un reloj pionero a prueba de rayones: 60 años después, el DiaStar Original se renueva. Un artículo de 1962 en Europa Star.
- ©Europa Star Archives
La innovación seguirá siendo crucial si Rado quiere defender su título de «Maestro de materiales» a largo plazo: «Vengo del mundo de la competición deportiva y he aprendido que incluso si rompes un récord, otro corredor eventualmente te alcanzará». usted”, dice Adrian Bosshard. “Siempre hay espacio para crecer: el plasma y las cerámicas de colores lo demuestran, al igual que el Nivachron resistente a campos magnéticos que equipa nuestros movimientos”.
“Siempre hay espacio para crecer: el plasma y las cerámicas de colores lo demuestran, al igual que el Nivachron resistente a campos magnéticos que equipa nuestros movimientos”.
-
- Lanzado en 1962, el icónico DiaStar Original de Rado renace con motivo de su 60 aniversario. El diseñador Alfredo Häberli ha creado una edición especial, enmarcada por un peinado Ceramos cepillado radialmente con ángulos pulidos. El movimiento automático Rado R764 garantiza una reserva de marcha de 80 horas.
La cerámica sigue siendo el terreno de juego particular de Rado. Otras marcas han adoptado el material, pero no en la misma medida. Esta estrategia bien definida también significa que el relojero se está alejando un poco de los canales de suministro tradicionales del sector y tiene un mejor control sobre su producción. Siempre que, por supuesto, pueda asegurar su suministro de materiales básicos, en un momento en que otras marcas están acumulando sus existencias de oro y acero antes de lo que será un invierno difícil para cualquier instalación que dependa de hornos de muy alta temperatura. Donde la energía se encuentra con la materia: esta es una forma adecuada de describir el proceso que da como resultado la creación de los relojes altamente individuales de Rado.
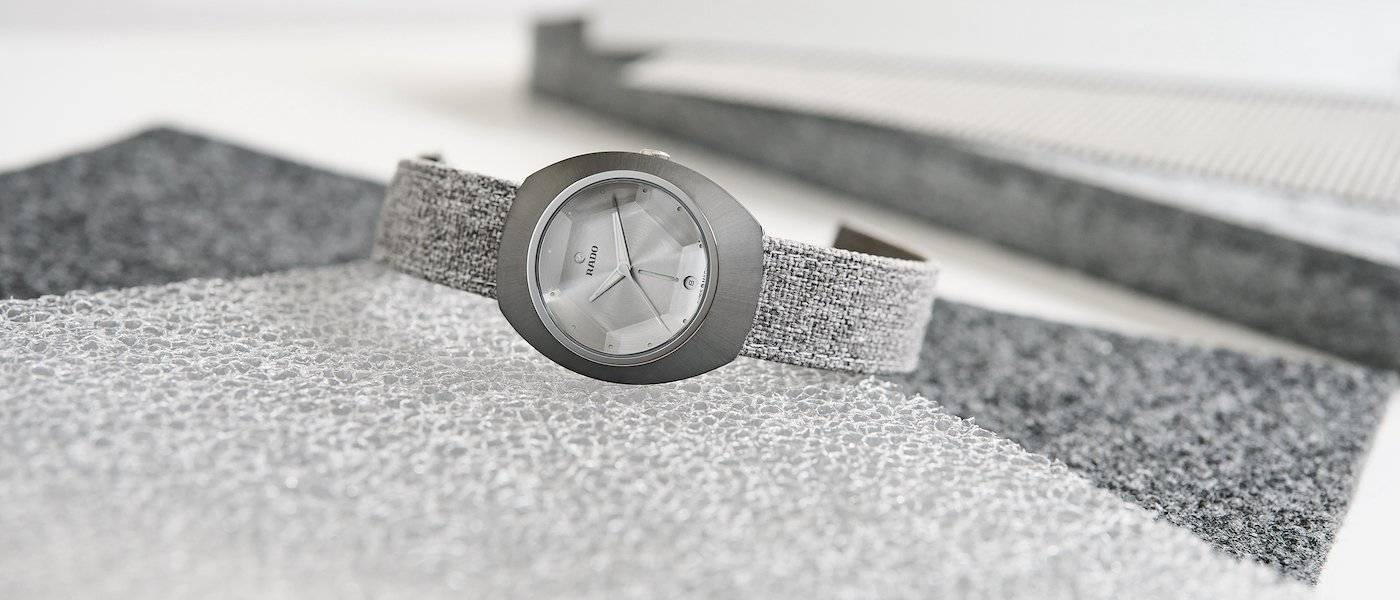
LAS ETAPAS DE LA PRODUCCIÓN CERÁMICA
-
- DISEÑO DEL MOLDE: el diseñador de la marca crea un molde a partir de bocetos.
-
- MOLDEO POR INYECCIÓN: el molde se coloca en el interior de la enorme máquina donde se lleva a cabo el proceso de inyección.
-
- SINTERIZACIÓN - Las cajas se colocan dentro de un horno especial, cocido a una temperatura extremadamente alta (1450°C). Durante muchas horas la cerámica se endurece por completo y adquiere su intenso color final y máxima dureza, mientras el polímero se evapora. Durante este proceso, la caja se encoge alrededor de un 25% hasta su tamaño final.
-
- MECANIZADO - Las dimensiones precisas finales se mecanizan con herramientas de diamante para lograr la precisión necesaria.
-
- PULIDO - Los componentes destinados a un brillo excepcional se sumergen en un baño de diminutos fragmentos de cerámica que vibran a alta frecuencia.
-
- CHORRO DE ARENADO: el chorro de arena de precisión se utiliza para producir un acabado mate con una suavidad uniforme.
-
- GRABADO: un láser graba números y marcas en el bisel, creando contornos y depresiones perfectos.
-
- HORNO DE PLASMA - Los componentes destinados al acabado de plasma cerámico de alta tecnología se someten a una nueva cocción en el horno. El color blanco inicial se transforma en un tono y acabado metálico permanente.
-
- LAQUEADO: los diminutos huecos creados por el láser se rellenan con una laca que se adhiere permanentemente a la cerámica una vez que se seca. Este delicado y diestro trabajo lo realizan los relojeros.
-
- CONTROL DE CALIDAD - Se realiza una rigurosa inspección para asegurar que el resultado final cumpla con los estándares de la marca.